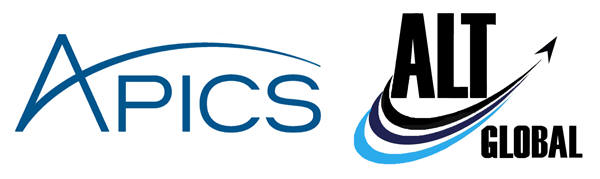
Chứng chỉ quốc tế
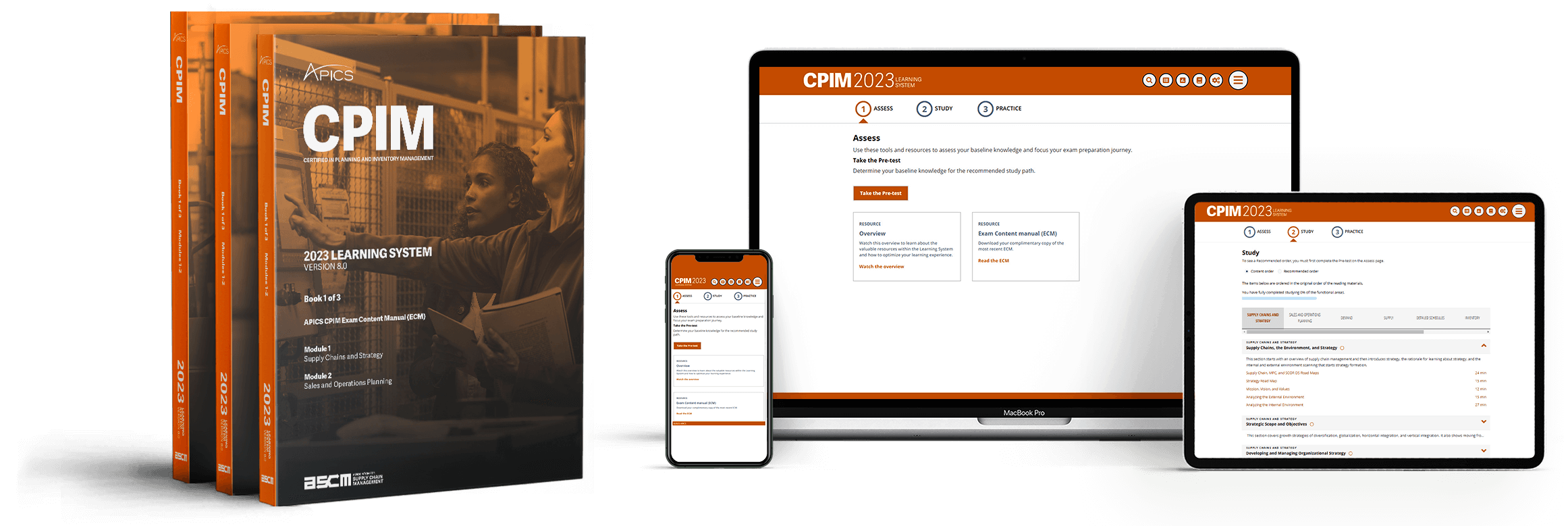
CPIM
CERTIFIED IN PLANNING AND INVENTORY MANAGEMENT
Thời lượng: 7 ngày
Địa điểm: HCMC
• Về CPIM – Certified in Planning and Inventory Management
Chứng chỉ APICS Certified in Planning and Inventory Management (CPIM) cung cấp kiến thức toàn diện, các phương pháp tốt nhất và tiêu chuẩn để cho phép các ứng viên ứng phó tốt hơn với sự gián đoạn nguồn cung, ứng phó với các thay đổi về nhu cầu và quản lý rủi ro chuỗi cung ứng.
Chứng chỉ CPIM được đánh giá là sự lựa chọn của hơn 87% nhà Quản lý cấp cao trong Chuỗi cung ứng, vượt qua vị trí thứ 2 và thứ 3 là Viện quản lý chuỗi cung ứng và Hội đồng chuỗi cung ứng, để trở thành sự lựa chọn hàng đầu và phổ biến nhất trên thế giới.
Hành trình học tập của học viên sử dụng Hệ thống học tập CPIM (CPIM learning systems) được thiết kế giúp người học xây dựng & phát huy tối đa điểm mạnh; nâng cao kiến thức chuyên môn; đảm bảo học viên nghiên cứu kiến thức và chuẩn bị cho kỳ thi.
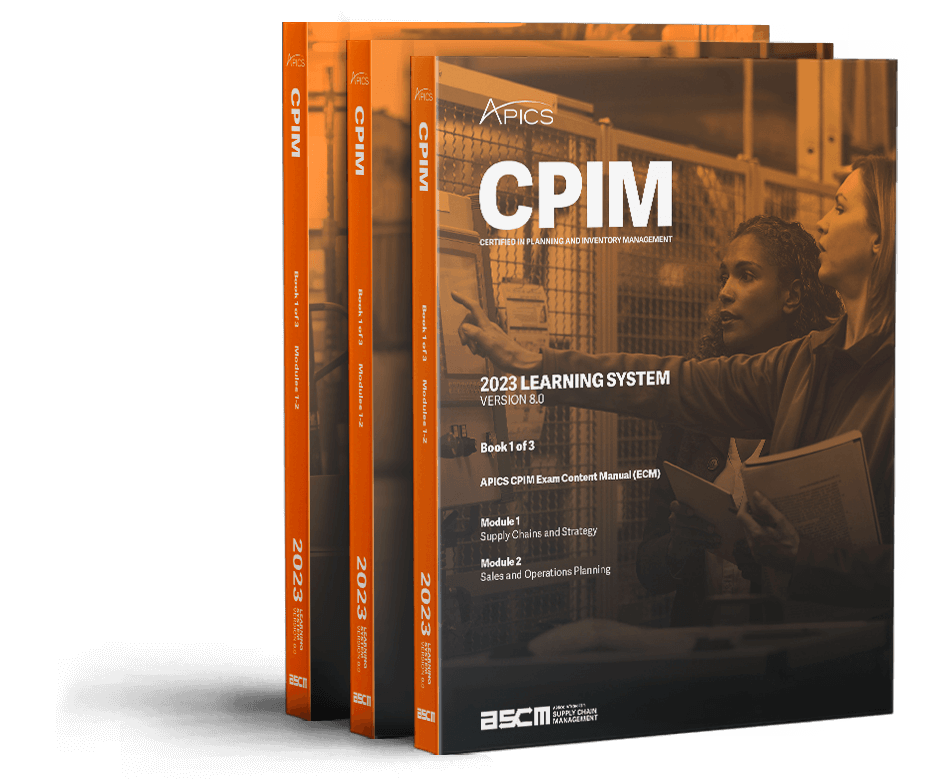
• Tại sao bạn nên có chứng chỉ Quốc tế CPIM
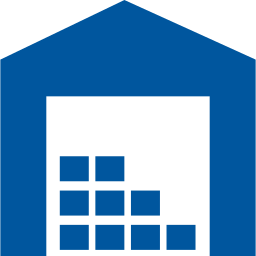
Giúp công ty của bạn đạt được trạng thái chuỗi cung ứng lý tưởng
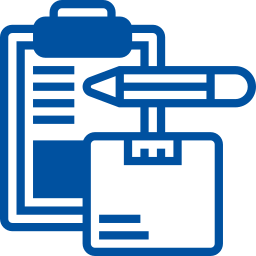
Cải thiện khả năng dự báo
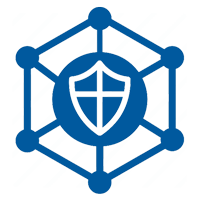
Làm việc hiệu quả hơn với hệ thống ERP của công ty

Cải tiến quy trình S&OP
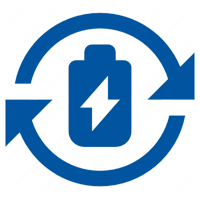
Quản lý và áp dụng hoạch định nguồn lực năng lực
• Đối tượng tham gia CPIM
Quản lý Chuỗi cung ứng
Nhà lập kế hoạch, mua hàng
Quản lý nguyên vật liệu
Nhà hoạch định sản xuất
Nhà tư vấn Chuỗi cung ứng
• Nội dung chương trình CPIM
MODULE 1: Supply Chains and Strategy
Section A: Supply Chains, the Environment, and Strategy
Section B: Strategic Scope and Objectives
Section C: Developing and Managing Organizational Strategy
Section D: Functional and Operational Strategies
Section E: Environments, Types, and Layouts
Section F: Performance Monitoring and KPIs
Section G: Risk Management
Section H: Capital Equipment and Facilities
Section l: Sustainability Strategies
MODULE 2: Sales & Operations Planning
Section A: S&OP Purpose and Process
Section B: Aggregate Demand and Supply Plans
Section C: Reconciling S&OP Plans
MODULE 3: Demand
Section A: Demand Management
Section B: Sources of Demand/Forecasting
Section C: Forecast Performance
MODULE 4: Supply
Section A: Creating and Validating the Master Schedule
Section B: IJsing and Maintaining the Master Schedule
Section C: Material Requirements Planning
Section D: CRP and Scheduling
Section E: Suppliers and Purchasing
Section F: Changes and Product Life Cycle Management
MODULE 5: Detailed Scheduless
Section A: Planning Detailed Schedules
Section B: Scheduling and PAC Methods
Section C: Creating Production and Service Schedules
Section D: Managing Detailed Schedules and Scheduling Materials
MODULE 6: Inventory
Section A: Inventory Planning
Section B: Inventory and Product Costs, Value, and Metrics
Section C: Itemized Inventory Management
Section D: Inventory Control
MODULE 7: Distribution
Section A: Planning Distribution
Section B: Replenishment and Order Management
Section C: Waste Hierarchy and Reverse Logistics
MODULE 8: Quality, Technology, and Continuous Improvement
Section A: Quality
Section B: Technology
Section C: Continuous Improvement
Hệ thống học tập CPIM là chương trình toàn diện kết hợp tài liệu bản in và trực tuyến, các bài kiểm tra thực hành trực tuyến và các công cụ học tập tương tác để đảm bảo học viên nghiên cứu kiến thức và chuẩn bị cho kỳ thi.
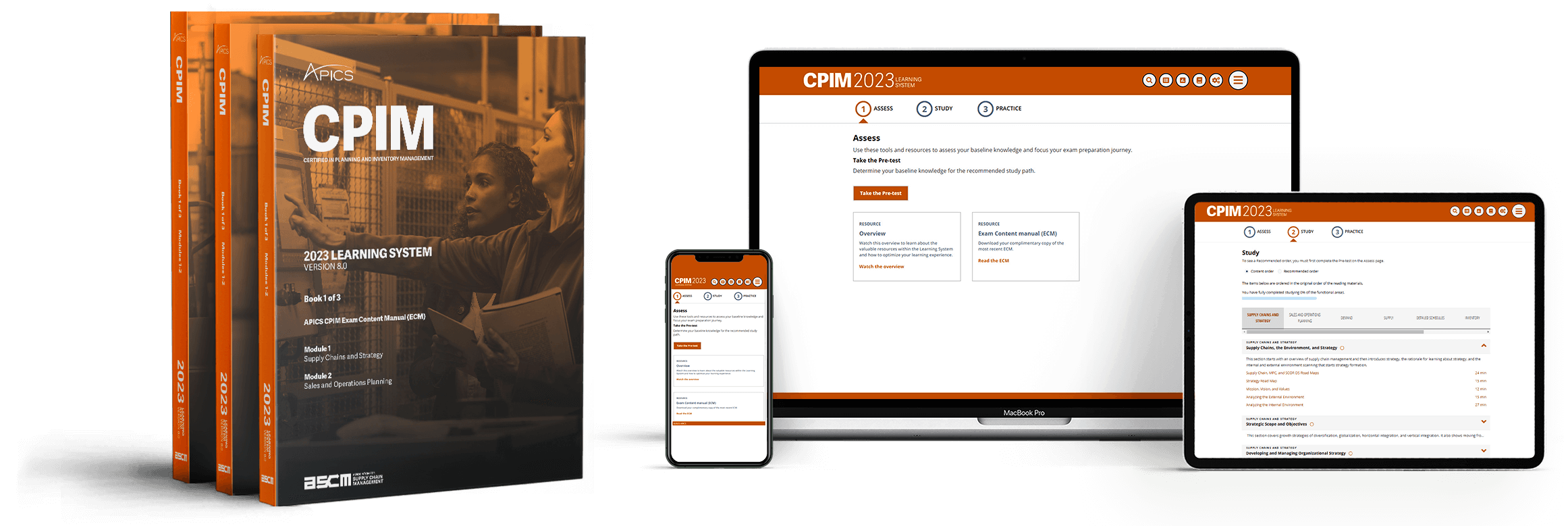
CPIM tự hào có một nền tảng học tập nâng cao, với tính trực quan bổ sung có thể giúp bạn giảm thời gian để đạt được chứng chỉ này. Các cập nhật cho nền tảng này bao gồm:
1. ĐÁNH GIÁ
- Hoàn thành bài kiểm tra thử để xác định kiến thức hiện tại của bạn và xác định các lĩnh vực cần cải thiện.
- Dựa trên điểm số bài kiểm tra thử, hệ thống học tập trực tuyến sẽ đề xuất kế hoạch học tập hiệu quả nhất.
2. NGHIÊN CỨU
- Trải nghiệm Nghiên cứu Cá nhân hóa ưu tiên nội dung dựa trên những lỗ hổng kiến thức và theo dõi sự tiến bộ của người tham gia thông qua điểm số và hoạt động của bài kiểm tra.
- Microlearning cho phép người tham gia tập trung vào các phân đoạn nội dung nhỏ hơn, sử dụng hiệu quả hơn thời gian có sẵn và đảm bảo họ hiểu rõ về từng chủ đề.
- Phương thức học tập mở rộng bao gồm tích hợp các video bổ sung để giúp đưa các khái niệm chính vào cuộc sống trong bối cảnh thế giới thực.
- Thuận tiện nhờ có thiết kế ưu tiên thiết bị di động và cung cấp quyền truy cập vào kiến thức thông qua bất kỳ thiết bị di động, máy tính bảng hoặc máy tính nào – 24/7.
- Hệ thống Học tập cung cấp quyền truy cập vào cả tài liệu kỹ thuật số và tài liệu in, cùng với các hoạt động học tập tương tác.
3. THỰC HÀNH
- Tham gia kỳ thi thực hành được thiết kế để giúp học viên có được kinh nghiệm với hình thức của kỳ thi trên máy tính.
- Truy cập thông tin bổ sung về kỳ thi chứng chỉ, các công cụ học tập và mẹo làm bài kiểm tra.
- Truy cập phần “My Progress” để theo dõi điểm bài kiểm tra và kết quả học tập của bạn.
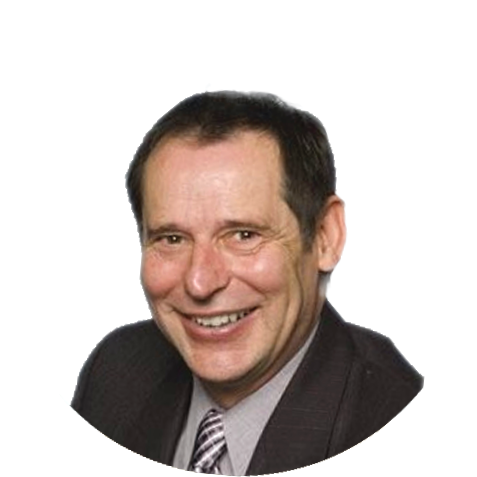
Mr. John Marson
APICS Master Instructor for CSCP, CPIM, CLTD
Ms. Nguyen Nhu Ngoc
APICS Associate Instructor for CSCP, CPIM
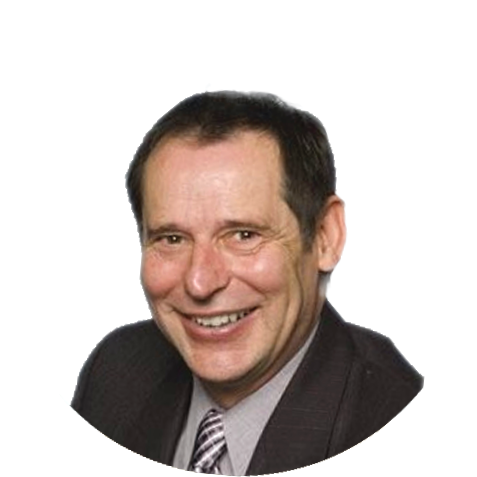
Mr. John Marson
APICS Master Instructor
Ms. Nguyen Nhu Ngoc
APICS Master Instructor
Ngôn ngữ giảng dạy: Tiếng Anh & Tiếng Việt
• Ms. Ngọc giảng dạy trực tiếp trên lớp
Địa điểm đào tạo: Tp. Hồ Chí Minh
ĐĂNG KÝ NGAY!
Hãy điền thông tin vào Form đăng ký tư vấn. VILAS sẽ liên hệ với bạn trong thời gian sớm nhất!
[VILAS cam kết những thông tin cá nhân của bạn chỉ được sử dụng với mục đích tham khảo cho đội ngũ tư vấn có thể đưa đến cho bạn những thông tin phù hợp nhất]