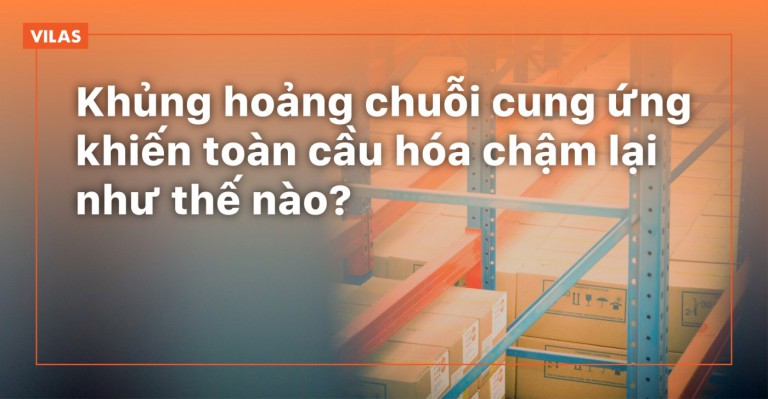
Khủng hoảng chuỗi cung ứng khiến toàn cầu hóa chậm lại như thế nào?
Khủng hoảng chuỗi cung ứng khiến toàn cầu hóa chậm lại như thế nào? Sự phát triển của Chuỗi cung
Hoạch định hàng tồn kho là công việc không thể thiếu của các nhà sản xuất. Hàng dư thừa sẽ chặn đứng dòng vốn của doanh nghiệp, chiếm diện tích sàn, tăng chi phí lưu trữ và tạo nên lãng phí. Mặt khác, stocks-out sẽ ảnh hưởng đến toàn bộ dòng chảy của Chuỗi cung ứng và ảnh hưởng đến doanh thu của tổ chức.
Chính vì vậy doanh nghiệp cần tìm hiểu 3 công cụ chính sẽ giúp hoạch định lịch trình sản xuất và lên kế hoạch nguyên vật liệu giúp giảm thiểu mức tồn kho không cần thiết đồng thời đảm bảo nguồn cung đầy đủ và kịp thời cho sản xuất: MPS, MRP, BOM. Trong đó, một “công cụ nhánh” vô cùng quan trọng giúp doanh nghiệp định mức nguyên vật liệu và công đoạn sản xuất chính là Bill of Material (BOM).
• Lập lịch trình sản xuất – là quá trình giúp nhà sản xuất lập kế hoạch sản phẩm và số lượng liên quan để sản xuất trong các giai đoạn nhất định. MPS chủ động ở chỗ nó thúc đẩy quá trình sản xuất về những sản phẩm nào được sản xuất và vật liệu nào được mua.
• Lịch trình sản xuất chính hình thành cơ sở của sự giao tiếp giữa bán hàng và sản xuất. Sử dụng MPS như một hợp đồng giữa bán hàng và sản xuất có nghĩa là việc bán hàng có thể tạo ra những đơn hàng có hiệu lực. MPS không phải là một kế hoạch cứng nhắc. MPS là một kế hoạch linh động và có thể được thay đổi khi có thay đổi về nhu cầu hoặc năng lực.
• Là một phần của hệ thống ERP tích hợp đầy đủ, MPS thường cung cấp chức năng lập kế hoạch quan trọng, trích xuất dữ liệu cung và cầu thực tế, cũng như dự báo, để đưa ra kế hoạch sản xuất chính xác và kịp thời giúp nhà sản xuất đạt được mục tiêu sản xuất và giảm thiểu chi phí. MPS cũng tính đến năng lực sản xuất của nhà máy trong tính toán của mình. Khi các đơn đặt hàng sản xuất đã được phân tích và phê duyệt, quy trình MRP được bắt đầu và các đơn đặt hàng có thể được tạo ra. MPS cũng cung cấp bảo vệ chống lại sự thiếu hụt, rối loạn trong việc lập kế hoạch bất ngờ và phân bổ nguồn lực không hiệu quả.
• Các kế hoạch MPS thường dựa trên đầu vào như đơn đặt hàng bán thực tế, đơn đặt hàng dịch vụ, tài nguyên có sẵn, mức tồn kho và hạn chế năng lực hoặc dự báo. Các dự báo này cung cấp cho các nhà sản xuất khả năng dự đoán nhu cầu sản phẩm và tính linh hoạt để điều chỉnh kế hoạch sản xuất dựa trên tính thời vụ, khuyến mãi và nhu cầu biến động đối với các mặt hàng cụ thể và / hoặc thành phẩm. Đầu ra từ MPS bao gồm số lượng của một mặt hàng sẽ được sản xuất, ngày đáo hạn và số lượng có sẵn để hứa.
Đạt mức độ dịch vụ khách hàng mong muốn
Sử dụng tài nguyên hiệu quả nhất
Duy trì mức độ tồn kho mong muốn
Đạt mức độ dịch vụ khách hàng mong muốn
Sử dụng tài nguyên hiệu quả nhất
Duy trì mức độ tồn kho mong muốn
MPS là mối liên kết giữa việc lập kế hoạch và sản xuất, được sử dụng làm cơ sở để tính toán năng lực và nguồn lực cần thiết để hoàn thành các kế hoạch sản xuất. MPS nằm ở trung tâm của hệ thống ERP (Enterprise Resource Planning) – hoạch định tài nguyên doanh nghiệp – sản xuất và kết nối với nhiều mô-đun bao gồm: Accounts Payable (AP), Accounts Receivable (AR), General Ledger (GL), Customer Relationship Management (CRM), Inventory, Purchasing, Lot Tracking and Human Resources (HR),… Một số lợi ích của MPS có thể kể đến như:
• Khả năng điều chỉnh biến động của nhu cầu trong khi giảm thiểu lãng phí;
• Ngăn chặn sự thiếu hụt và lập kế hoạch rủi ro;
• Cải thiện hiệu quả trong vị trí của các nguồn lực sản xuất;
• Cung cấp kiểm soát chi phí hiệu quả hơn và ước tính chính xác hơn về yêu cầu vật liệu và ngày giao hàng;
• Giảm thời gian thực hiện;
• Cung cấp một ống dẫn truyền thông hiệu quả với đội ngũ bán hàng cho mục đích lập kế hoạch.
• Materials Requirements Planning – MRP (Lập kế hoạch yêu cầu vật liệu) là một kế hoạch sản xuất, lập kế hoạch và kiểm soát hàng tồn kho được sử dụng để quản lý các quy trình sản xuất. MRP vẫn là lựa chọn tốt nhất trong môi trường khá ổn định và dựa trên dự báo như Make-To-Stock (MTS). MRP cũng có thể là một lựa chọn tốt cho một số tình huống đặt hàng Make-To-Order (MTO) khi một lô sản phẩm được tiến hành sản xuất sau khi đặt hàng.
Đảm bảo nguyên liệu có sẵn cho sản xuất và sản phẩm có sẵn để giao cho khách hàng
Duy trì mức vật liệu và sản phẩm thấp nhất có thể trong kho hàng
Lập kế hoạch hoạt động sản xuất, lịch giao hàng và hoạt động mua hàng
Đảm bảo nguyên liệu có sẵn cho sản xuất và sản phẩm có sẵn để giao cho khách hàng
Duy trì mức vật liệu và sản phẩm thấp nhất có thể trong kho hàng
Lập kế hoạch hoạt động sản xuất, lịch giao hàng và hoạt động mua hàng
MRP có trách nhiệm cân bằng giữa cung và cầu sản xuất. Đây là một kế hoạch duy nhất xử lý cả lịch trình cung ứng mua và sản xuất để đảm bảo các kích cỡ lô khác nhau và số dư tồn kho tối thiểu.
• Chức năng MRP cho phép các kế hoạch lặp lại toàn cầu, mô phỏng kịch bản cung ứng và giảm thời gian chu kỳ lập kế hoạch;
• So sánh thời gian sản xuất với thời gian sản xuất để đảm bảo dễ dàng có sẵn;
• Cải thiện hiệu suất cửa hàng, tối ưu hóa mọi nguồn lực;
• Đảm bảo hàng hóa được giao cho khách hàng đúng thời gian;
• Với mức tồn kho giảm và sử dụng tối đa tài nguyên, MRP tạo điều kiện cho năng suất.
• Định mức nguyên vật liệu (Bill of Material, viết tắt là BOM) là một danh sách các nguyên liệu, phụ lắp ráp, lắp ráp trung gian, tiểu hợp phần, các bộ phận (chính các bộ phận đó cũng sẽ sỡ hữu cho riêng mình một BOM), và số lượng của mỗi bộ phận cần thiết để sản xuất một sản phẩm cuối cùng. Một BOM có thể được sử dụng để liên lạc giữa các đối tác sản xuất hoặc giới hạn trong một nhà máy sản xuất và được xem là thành tố quan trọng nhất trong MRP. Dưới MRP, BOM đóng vai trò như một khung sườn giúp toàn bộ hệ thống Planning hoạt động.
• Một BOM có thể định nghĩa các sản phẩm khi chúng được thiết kế (Engineer Bill of Materials), được đặt hàng (sales bill of materials), được xây dựng (manufacturing bill of materials) hoặc được bảo trì (service bill of materials). Các loại BOM khác nhau phụ thuộc vào nhu cầu kinh doanh và mục đích sử dụng mà chúng dự định sử dụng. Trong các ngành công nghiệp chế biến, BOM còn được gọi là công thức hoặc danh sách thành phần. Cụm từ ” Định mức nguyên vật liệu ” (hoặc “BOM”) thường được các kỹ sư sử dụng như một tính từ để chỉ cấu hình sản xuất hiện tại của sản phẩm, phân biệt với các phiên bản được sửa đổi, cải tiến, đang nghiên cứu hoặc trong quá trình thử nghiệm.
• Đối với các công ty thuê ngoài hoạt động sản xuất, điều đặc biệt quan trọng là tạo ra một BOM chính xác và luôn được kiểm soát cập nhật sửa đổi. Bất cứ khi nào BOM được bàn giao cho nhà sản xuất hợp đồng (CM) hoặc nhà cung cấp, nó phải chính xác và hoàn thiện để tránh sự chậm trễ do các trục trặc trong sản xuất.
Tổng hợp các thành phần & bộ phận của sản phẩm
Quản lý và định lượng chính xác các nguồn lực
Căn cứ cho việc ra quyết định lựa chọn nhà cung cấp
BOM đóng vai trò như một bản hướng dẫn giúp doanh nghiệp có thể nắm bắt các nguồn lực và nguyên liệu cấu thành sản phẩm của mình. Với một BOM hoàn thiện doanh nghiệp có thể đạt được những lợi ích như:
• BOM đơn giản giống như một “Quyển sách hướng dẫn” hoặc một “danh sách mua sắm” nên nó sẽ tối ưu hóa quy trình thu mua nguyên vật liệu đầu vào. Lúc này bộ phận purchasing chỉ việc làm đúng nhiệm vụ của mình chính là mua hàng theo như BOM đã được duyệt;
• Khi sỡ hữu một BOM hoàn thiện, các nhà quản trị đã có tất cả dữ liệu họ cần để lập ra kế hoạch sản xuất và nguyên vật liệu phù hợp;
• Với một danh sách rõ ràng về vật liệu, số lượng và hàng tồn kho, việc thiếu hụt nguyên vật liệu cho sản xuất do đặt hàng sẽ được hạn chế;
• Ngoài ra, một BOM rõ ràng cũng sẽ giúp bộ phận R&D có thể tối ưu hóa các quy trình cái tiến, phát triển sản phẩm mới cho doanh nghiệp.
Trong thực tế, MRP sẽ sử dụng MPS cùng với BOM để tạo ra kế hoạch cung cấp theo từng giai đoạn cho các yêu cầu về bán thành phẩm và các thành phần. Cả 3 yếu tố đều đóng một vai trò tất yếu của mình trong hoạch định lịch trình sản xuất và lên kế hoạch nguyên vật liệu nhằm tránh tình trạng stock-out cũng như việc sản xuất dư thừa tạo nên những lãng phí không đáng có. Tìm hiểu về 3 công cụ này, doanh nghiệp sẽ có thể nắm bắt được các cơ sở ra quyết định phù hợp nhằm đảm bảo quá trình sản xuất liền mạch và tối ưu hóa các chi phí lưu trữ & sản xuất, đồng thời ứng dụng phù hợp đối với từng môi trường sản xuất của doanh nghiệp.
(1) Hegge, H. M. H., & Wortmann, J. C. (1991). Generic bill-of-material: a new product model. International Journal of Production Economics, 117–128.
(2) J.A. Orlicky, G.W. Plossl, O.W. Wight (2003). Structuring the Bill of Material for MRP.
(3) OtiproERP. Inventory Management 101 – The Master Production Schedule (MPS) Explained. Available at: https://www.optiproerp.com/blog/inventory-management-101-master-production-schedule-mps-explained/ [Accessed 4 April 2020].
(4) OtiproERP. IHow Can Material Requirement Planning Create A Difference In Manufacturing. Available at: https://www.optiproerp.com/in/blog/how-can-material-requirement-planning-create-a-difference-in-manufacturing/ [Accessed 4 April 2020]
Biên soạn và tổng hợp: Vinh Trinh
Layout & Graphic Design: Vinh Trinh
Khủng hoảng chuỗi cung ứng khiến toàn cầu hóa chậm lại như thế nào? Sự phát triển của Chuỗi cung
Sự lây lan trên của những biến chủng coronavirus mới vào năm 2021 đặt ra những thách thức lớn cho nỗ lực quản trị vận hành chuỗi cung ứng
FIATA văn bằng quốc tế về Logistics và Quản trị chuỗi cung ứng GIỚI THIỆU FIATA – Liên đoàn các
Góc nhìn khác về toàn cầu hóa qua sự đóng băng của Chuỗi cung ứng từ vũ hán TÓM TẮT